Wrapping paper is one item that everyone wants and needs during the holiday season. In fact, people spend an estimated $2.6 billion in the United States every year on wrapping paper. While decorated paper is the most common type of wrapping paper nowadays, fabric wrapping cloths, known as ‘furoshiki’ in Japan and ‘bogaji’ in Korea, were some of the first instances of this gift wrapping method in history. But, with such a long and festive history, do we really know how this product is designed, developed, and shipped just in time for the winter season?
As part of the new supply chain journey series by Stimulus, we’ve chosen to break down the entire journey of wrapping paper from printer to store in order to show exactly what skill and creativity goes into every paper roll. Without further ado, let’s analyze this holiday staple and see what makes it so incredible below.
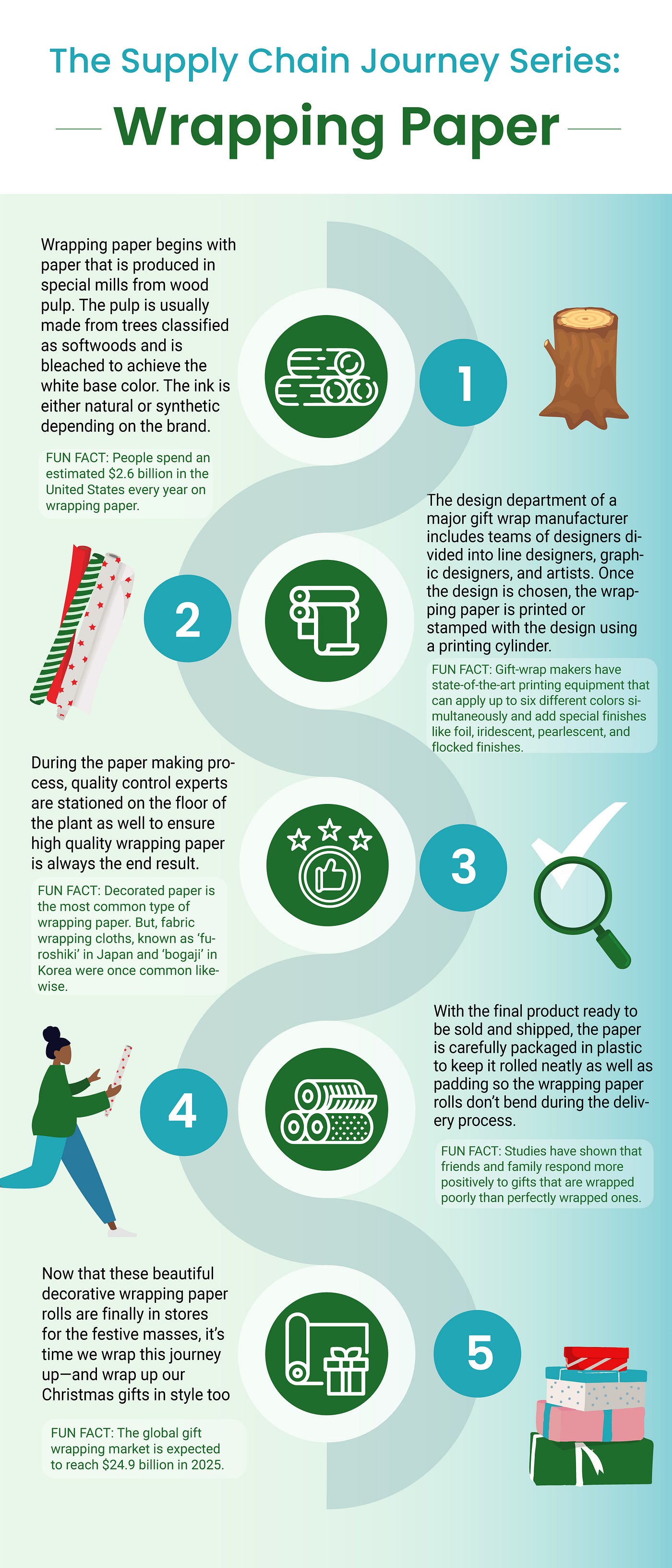
Materials
Wrapping paper begins with paper that is produced in special mills from wood pulp. The pulp is usually made from trees classified as softwoods and is bleached to achieve the white base color.
When it comes to the designs on the paper, special inks are used. The ink is either natural or synthetic depending on the brand. However, nowadays, synthetic is far more common as it can help to mass produce wrapping paper for major retailers such as Walmart.
Design and Manufacturing
The success of a certain wrapping paper brand is dependent on the designs it chooses to create. The design department of a major gift wrap manufacturer includes teams of designers divided into line designers, graphic designers, and artists. The most popular designs are typically pop culture characters and traditional gold, red, and green holiday colors.
Once the design is chosen, the wrapping paper is printed or stamped with the design using a printing cylinder. Gift-wrap makers have state-of-the-art printing equipment that can apply up to six different colors simultaneously and add special finishes like foil, iridescent, pearlescent, and flocked finishes.
Quality Control
All workers are responsible for product quality during the production process. However, during the paper-making process, quality control experts are stationed on the floor of the plant as well to ensure high quality wrapping paper is always the end result.
However, when it finally ends up in the hands of consumers, the quality of the paper may not matter as much as previously assumed. In fact, studies have shown that friends and family respond more positively to gifts that are wrapped poorly and cheaply.
Shipping
With the final product ready to be sold and shipped, the paper is carefully packaged in plastic to keep it rolled neatly as well as padding so the wrapping paper rolls don’t bend during the delivery process.
The shipping containers must also remain dry and not deal with changing temperatures as ink bleeding can occur in these situations.
Wrap it Up!
Now that these beautiful decorative wrapping paper rolls are finally in stores for the festive masses, it’s time we wrap this journey up — and wrap up our Christmas gifts in style!
With a lengthy and highly creative supply chain such as this, it’s no wonder why the global gift wrapping market is expected to reach $24.9 billion in 2025.
Stay tuned for more supply chain journeys to come, and feel free to watch the ‘How It’s Made: Wrapping Paper’ episode below to see some more of this journey in action: